Most businesses that acquire or use chemicals are aware of their legal obligations in terms of obtaining and preserving a safety data sheet for those items. However, many companies are unsure what to do with the information included in the safety data sheets they have obtained.
All the information supplied in an SDS should be compiled to help the company personnel understand how they must handle a substance and what they must do in the event of a mishap. Therefore, this article will offer you a thorough understanding of safety data sheet management and the tips you must follow to manage these files successfully.
Table of Contents
1. Appoint An In-Charge
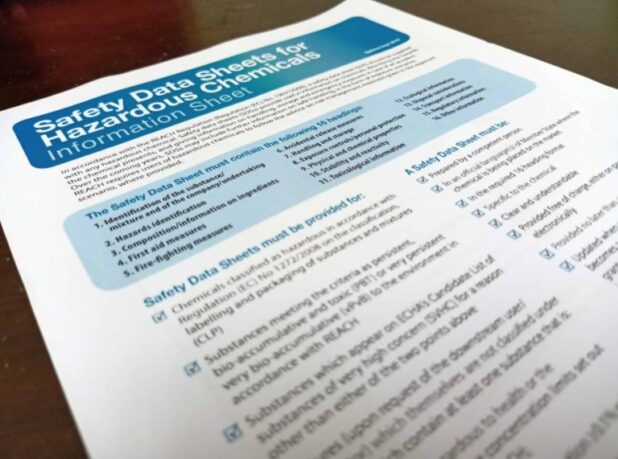
Safety data sheet management entails much more than simply putting sheets in a binder. They need to be reviewed by someone regularly and kept updated on the products added to the organization’s list.
While OSHA will not hold you responsible for any errors or missing information on your safety data sheet, they will expect you to maintain the sheets in good faith from the manufacturer or importer.
Once you have accepted the SDS, it indicates that there were no blank spaces or incorrect information in the material you received. Someone from your team should review them to ensure they’re complete and accurate.
If you do not receive a safety data sheet or a corrected one from a chemical manufacturer or importer, make sure to contact your local OSHA area office for assistance.
All requests or corrections should be documented, according to OSHA. You must produce documentation of your request if an OSHA inspector goes through your paperwork while you wait for the form or revised form, or you will be deemed in non-compliance.
2. Use Safety Data Sheet Management Tools
Most manufacturers have hundreds of archived safety data sheets in their database, making it challenging and time-consuming for employees to locate a specific Safety Data Sheet. When looking for an old or amended, things get even more tricky. By making it easy to identify, update, and communicate across corporate silos, using SDS management software reduces the impediments in your safety data sheet plan.
A safety data sheet management software is built with the most stringent data quality controls in mind, ensuring that your company meets the Globally Harmonized System’s strict accuracy requirements. When it comes to categorizing and conveying chemical dangers in the workplace, even the most minor details matter, and safety data sheets log everything. If you wish to gain more information on SDS management tools, click on this site.
3. Keep It Updated
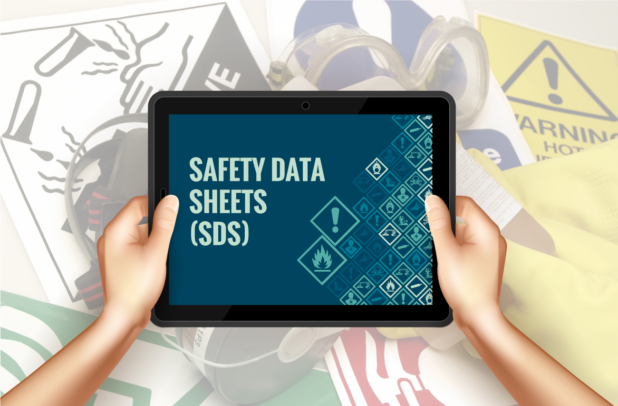
A good collection of Safety Data Sheets is one that is current and specific to the hazardous items present. Products and chemicals utilized in your facility may change over time. Changes such as the following may necessitate revision:
- The transition from one product to another (i.e., non-hazardous degreaser to a corrosive degreaser)
- Changes in product ingredients by the manufacturer
- There have been some significant new discoveries.
In addition, any new chemicals introduced to the workplace will require a safety data sheet added to the company’s catalog, and any compounds that are no longer in use should be deleted. All SDS records should be managed and kept by one person or a small group inside your firm.
4. Keep Old Safety Data Sheets In A Safe Place
Employers must keep safety data sheets or some other records of the chemical’s identity, where and when it was used, for 30 years beyond the end-use date, according to OSHA Standard 29 CFR, 1910.1020, Access to Employee Exposure and Medical Records.
A complete chemical inventory list with exact date and location information, as well as a safety data sheet, satisfy the criteria. To put it another way, if a corporation decides to preserve the safety data sheet, that is all the information they are required to keep. If they don’t want to keep the safety data sheet, they’ll have to provide further information on where and when the chemical was utilized.
Former employees might use the information on the safety data sheet to diagnose difficulties that may have arisen due to their exposure. It can also help the employer indemnify themselves by presenting documentation of what was (and wasn’t) known about a hazard when a worker was hired. Companies can also use it to test employee exposure.
Keeping both the safety data sheet and information regarding when and where it was used is an excellent best practice. A robust electronic SDS management system can easily accomplish this duty without the need for thousands of paper papers to be stored for years.
5. Train Your Employees
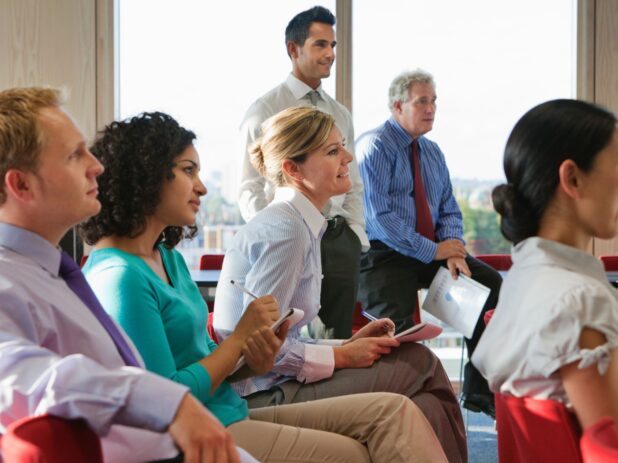
Your staff must be adequately trained on where and how to access your safety data sheets, whether digital or hard copy. Safety data sheet information is intended to be used not just when using a hazardous chemical but also in the event of an accident.
If properly trained, safety data sheet data can be an integral part of overall hazardous material and workforce safety. Employees familiar with safety data sheet information can make better decisions on the use of personal protective equipment (PPE), appropriate chemical handling, and proper disposal or storage techniques.
6. Toxic Materials Should Be Labeled Appropriately
It is critical to include the appropriate labels for products that may become harmful. Please make sure they’re in a visible location and that they’re not tampered with in any manner. While a vast list of hazardous compounds must be labeled, not all of them are entirely dangerous. You must read about the hazardous and non-hazardous compounds extensively to make an accurate safety data sheet.
Conclusion
The safety data sheet is a valuable resource for workers and anyone responsible for controlling the workplace’s risks associated with chemical handling. Before working with a hazardous chemical, personnel should read the safety data sheet thoroughly and comprehend its contents so that it can be safely stored, handled, and used by everyone. The well-being of your employees, customers, and compliance all depends on how successfully you manage your Safety Data Sheet collection.